In a context of fierce competition, environmental imperatives, and changing consumer expectations, manufacturing harnessed technology to boost labour productivity by an incredible 75% in the last 25 years.
In the same period, and facing similar challenges, the construction sector has hardly moved at all.
But the opportunities are there. From BIM to smart sensors and IoT connectivity, the potential for improving product and process efficiency, project management and innovation is huge.
Unleashing this potential requires a long-term vision and a spirit of collaboration between all stakeholders, who will all benefit from better safety, efficiency, visibility, and a lower carbon footprint.

Radboud Wijnen
Digital Transformation Officer
Share this article
Better collaboration with BIM and IoT
While most players in the construction industry are still using BIM for basic designs and drawings, Consolis is now fully 3-D for some projects and targeting to go beyond: aiming to incorporate time management (4-D) and budget calculation (5-D) into all its models. This will mean more collaboration and better long-term planning with other project partners.
And when all actors are BIM-compatible – be they architects, engineers, project managers, and building owners – the ability to collaborate at all levels will help them plan together with greater flexibility and reduced risk, and to innovate with unprecedented freedom.
Using BIM in all dimensions requires a higher capacity to transform raw data from sensors and IoT connected devices into usable information, which Consolis is doing on major construction projects.
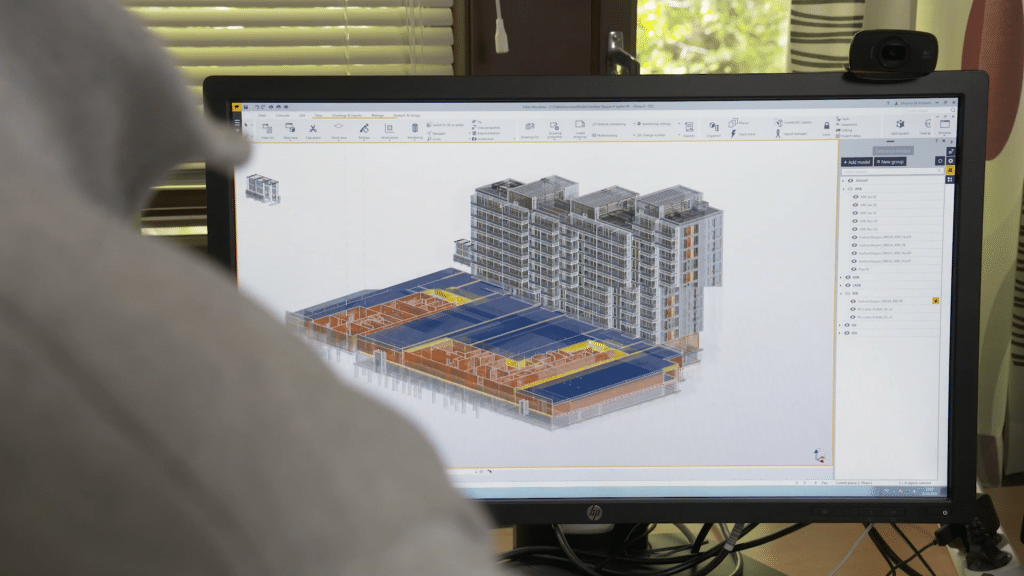
Connected pre-cast tunnel segments
The Grand Paris Express is a vast infrastructure project to upgrade the public transport system in the greater Paris area. With 200km of new rail lines, Consolis is the leading supplier of pre-cast tunnel segments and railway sleepers.
The Consolis Connect Track & Trace solution includes RFID chips embedded in each pre-cast tunnel segment, which can be identified as individual products throughout their lifecycle, across locations and trading partners, making it possible to locate, manage, and ship them with greater efficiency, assuring quality control and enhancing customer satisfaction.
Modularity will deliver long into the future
Embedded chips, combined with a fully collaborative BIM approach, can transform our relationships with buildings in other ways.
The “Circle House” project in Denmark, which consists of 60 general housing units outside Aarhus and should be completed in 2002, is a scalable demonstration project that proves the value of circular construction.
Electronic chips embedded in each precast element contain a unique identification “passport”, allowing all data in that element’s lifecycle, from production through to transport, construction, use and maintenance, to be collected and modelized.
When the building is eventually decommissioned, each element will be reused in new building projects.
A similar project is the experimental “Circular Viaduct” in the Netherlands. Completed in 2019, this viaduct has a span of 20 meters and consists of 40 concrete elements, each with an embedded chip.
Information from the chips helped control inventory and supply chain management during the building phase, and greatly simplified construction. Being fully modular, the entire structure is designed to be disassembled, moved and reused to create an entirely new structure.
Projects like this require all players to adopt the mindset that technology allows for better long-term strategic collaboration, while giving owners and users improved safety and efficiency.
This future is happening right now, and Consolis is leading the way.